That's the way the concrete crumbles
Reinforced concrete has been one of the materials that have revolutionized the construction industry, paving the way for the modern era in architecture. The possibility to be easily poured and moulded into any shape, accompanied by its strength, durability, and low price, makes it a favourable choice for the majority of structures built in the last century. In existing residential buildings, it forms a number of structural elements such as walls, slabs, columns, support beams, posts, and staircases.
Early 20th-century engineers thought reinforced concrete structures would last a very long time – even up to 1,000 years. In reality, their life span is significantly shorter, depending on the quality of the production and maintenance, it can last for 50 – 100 years. Although we expect a building to survive for several decades, the process of decay can start in as little as 10 years. Over time, concrete is susceptible to deterioration due to several factors which could harm the material, reduce its strength and create unsafe conditions.
The main degradation of a concrete structure is caused when water, air or salt come in contact with the embedded reinforcing steel, leading to internal damage in the form of corrosion. In addition to decay of the iron reinforcement itself, the rust affects the surrounding concrete, causing cracking, delamination and spalling. As the material cracks and crumbles, more water and air contact the reinforcing steel, causing even greater damage.
Worse still, earlier substandard construction methods have contributed to accelerating early decay. The common use of sea salt or other chemicals, meant to speed up the hardening process, provoke the steel reinforcements to gradually corrode over time. Moreover, the incorrect choice or positioning of the reinforcement bars causes cracks, which open the way for additional water infiltration and eventual corrosion.
In the case of mid-20th century buildings, although most of the concrete elements were being waterproofed, a lack of elasticity in their membranes resulted in severe cracks. Additionally, the detailing of some elements like balustrades often included joints to the slabs which were drilled also through the waterproofing. Such fractures or punctures of the membranes make the waterproofing layer penetrable, leading to an even faster decay.
Notwithstanding the above, one solution is concrete restoration, which allows us to fix the structures and bring them back to their original quality. This way, we can stop the degradation process and ensure the construction remains in good condition for years to come. In addition to improving the structural and safety aspects, the repair work can also enhance the aesthetics and market values of the property, providing a positive return on investment.
Many owners believe that in order to repair structural damage, it is obligatory to replace or remove entire sections of the building. While it may be necessary in some cases of extreme damage, it is certainly not the only solution to such problems.
Nowadays, with new techniques being developed constantly, there are many efficient ways of restoring damaged concrete elements. One such example is “Galvashield Fusion T2”, a method which repairs concrete degradation and crumbles without complex wiring or external supplies of electricity.
The procedure consists of drilling holes in the concrete and inserting type 2 anodes, which attacks the cause of corrosion with a powerful dose of electrochemical treatment. This way the structure is being preserved without the need of additional monitoring or maintenance. Moreover, “Galvashield Fusion T2” provides the flexibility of application based on the required need, as it can repair the entire structure or just the extreme corrosion hotspots.
With every restoration case being different, the corresponding treatments vary as well. That being said, the key has always been a timely detection and intervention to avoid complicated and expensive procedures, or irreparable damage.

Why redevelopment?
A building is never truly finished; it can always be re-adapted and transformed to take upon a new form or function. Recycling architecture has been a common practice throughout history, and in many cases, it has led to the preservation of a large part of our current cultural heritage. Read more.

That's the way the concrete crumbles
Early 20th-century engineers thought reinforced concrete structures would last a very long time – even up to 1,000 years. In reality, their life span is significantly shorter, depending on the quality of the production and maintenance.
The story behind redevelop
“It takes 65 years for a new energy-efficient building to save the amount of energy that an adaptive reuse project does. redevelop is a strategic design firm that develops and implements sustainable strategies to develop post-war buildings for contemporary use.”

Heating and cooling efficiency
Heating and cooling in buildings and industry take the lead in the EU’s total energy consumption. Notably, 75% of heating and cooling is still generated from fossil fuels. As such, they play a crucial role in a country’s transition towards greater energy efficiency and decarbonization.
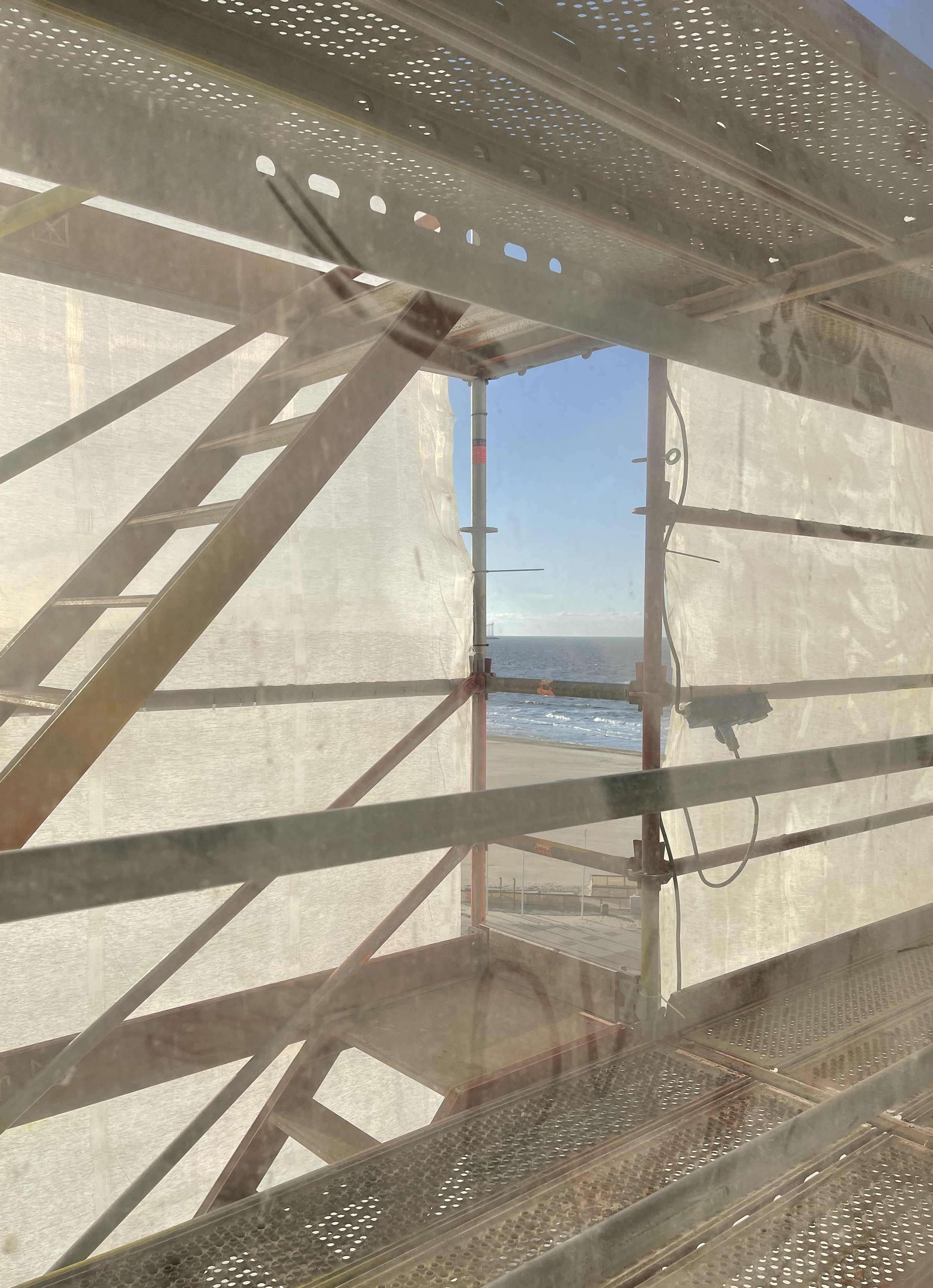